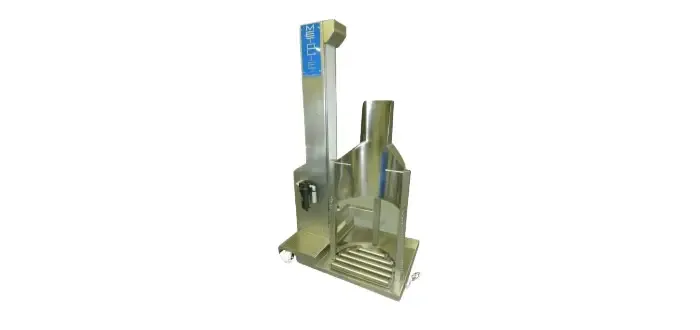
How to Reduce Costs with Bulk Material Handling Equipment?
Reducing costs with bulk material handling equipment is about smart choices and careful planning. Investing in automation can really streamline operations, cutting down on labor expenses and boosting efficiency. It’s also wise to keep up with regular maintenance so equipment stays in good shape—no one wants unexpected breakdowns that cause delays. Choosing the right gear for your needs is crucial too; it’s not just about upfront costs but the total cost over time. Besides, training your workforce ensures they’re working efficiently and safely while optimizing their schedules can save more cash. Don’t forget energy efficiency plans and evaluating supply chains to spot any cost-cutting opportunities!
1. Invest in Automation to Cut Costs
Investing in automation can significantly reduce costs in bulk material handling equipment. Automated systems like conveyors and automated guided vehicles (AGVs) streamline operations, minimizing the need for manual labor. For example, a facility that uses AGVs can efficiently transport materials without constant human oversight, leading to lower labor expenses and faster processing times. Additionally, implementing software for inventory management helps optimize the flow of materials. This reduces waste and ensures that resources are used efficiently, which ultimately contributes to cost savings.
2. Importance of Regular Maintenance
Regular maintenance of bulk material handling equipment is crucial for avoiding unexpected breakdowns that can halt operations and lead to significant costs. Establishing a routine maintenance schedule helps ensure that equipment is functioning optimally, reducing the risk of costly downtime. Additionally, using predictive maintenance techniques, such as IoT sensors, allows companies to monitor the health of their equipment in real-time, enabling proactive repairs before failures occur. For example, a manufacturing plant that implements a predictive maintenance system may identify a worn-out component before it causes a major failure, saving time and money in repairs and lost production. This preventive approach not only extends the lifespan of the equipment but also helps maintain consistent productivity levels, ultimately contributing to lower operational costs.
3. Optimize Your Equipment Selection
Selecting the right bulk material handling equipment is crucial for reducing costs. First, it’s important to match the equipment with the specific materials you’ll be handling. For example, using a conveyor system for loose bulk materials like grains differs from using a vacuum system for powders. Each material type has its own handling requirements, which can influence efficiency and costs.
Additionally, consider the total cost of ownership (TCO) when making your selection. This includes not only the initial purchase price but also maintenance and operational costs over the equipment’s lifetime. For instance, while a high-capacity loader might have a steep upfront cost, its efficiency in moving materials could lead to significant savings in labor and time in the long run.
Evaluating equipment based on performance metrics, like throughput and energy consumption, can also inform better decisions. Opt for equipment that offers flexibility and adaptability to various materials, which can help avoid the need for multiple machines and reduce overall expenses.
4. Training for Efficient Workforce Management
Training is crucial for maximizing the efficiency of your workforce in bulk material handling. By investing in comprehensive training programs, you ensure that employees are well-versed in operating equipment safely and effectively. For instance, a well-trained operator can significantly reduce the risk of accidents, which can lead to costly downtime and injuries.
Moreover, effective training helps workers understand the best practices for managing the flow of materials, optimizing their use of time and equipment. Consider a situation where operators are trained to use automated systems like conveyors and AGVs; their ability to navigate these technologies seamlessly can enhance productivity and reduce labor costs.
Additionally, workforce scheduling should align with operational needs. By analyzing peak times and workload requirements, you can optimize staff schedules to ensure that employees are present only when necessary. This approach not only cuts labor costs but also enhances overall efficiency. For example, if your operations see a surge in demand during certain hours, training staff to adjust their schedules accordingly can prevent bottlenecks and maintain workflow.
- Develop a comprehensive training program for all employees.
- Implement cross-training to enhance team flexibility.
- Encourage safety training to prevent workplace accidents.
- Schedule regular refreshers and updates to training content.
- Utilize mentorship programs to foster knowledge sharing.
- Evaluate training effectiveness through performance metrics.
- Create a feedback loop for continuous improvement in training.
5. Enhance Energy Efficiency Practices
Improving energy efficiency is a vital strategy for reducing costs in bulk material handling operations. Investing in energy-efficient equipment, like variable frequency drives (VFDs) for motors, can significantly lower energy consumption. These devices adjust motor speed and torque, ensuring they only use the power needed for a given task. Additionally, consider upgrading to energy-efficient lighting systems that not only cut down on electricity bills but also improve workplace safety and productivity.
Monitoring energy usage is equally important. By tracking consumption patterns, companies can identify peak usage times and implement strategies to reduce energy waste. For example, scheduling high-energy tasks during off-peak hours can lead to lower utility rates. Simple practices, such as ensuring that equipment is turned off when not in use and maintaining proper insulation in storage areas, can also contribute to energy savings.
6. Optimize Material Handling Layout
An efficient material handling layout is crucial for minimizing costs and maximizing productivity. Begin by analyzing the flow of materials through your facility. The goal is to create a layout that reduces unnecessary movement and transport. For instance, if your raw materials are stored far from the production line, this can lead to wasted time and increased labor costs. By positioning storage closer to the point of use, you can streamline the process.
Incorporating lean principles can further enhance your layout. Techniques like value stream mapping can help identify bottlenecks and unnecessary steps in your workflow. For example, if workers are frequently traveling back and forth between different areas, consider reorganizing the layout to bring those functions closer together. This not only saves time but also reduces the risk of accidents and improves overall safety.
Additionally, consider using modular systems that can be adapted as your business grows or changes. Flexibility in your material handling layout allows for adjustments without significant investments. By continually evaluating and optimizing your layout, you can maintain efficiency and reduce costs over time.
7. Leverage Bulk Purchasing Agreements
Bulk purchasing agreements can significantly reduce costs associated with raw materials in bulk material handling. By consolidating orders with suppliers, companies can negotiate better pricing based on volume, which often leads to substantial savings. For example, if a manufacturing facility typically orders 1,000 tons of steel per year, setting up a bulk agreement for 5,000 tons could reduce the cost per ton by a notable percentage. This strategy not only lowers the purchase price but can also minimize shipping costs due to fewer, larger deliveries. Furthermore, establishing long-term relationships with suppliers through these agreements may lead to additional benefits, such as priority service and improved payment terms. Overall, leveraging bulk purchasing agreements is a smart way to enhance budget efficiency and strengthen supply chain reliability.
8. Implement Lean Manufacturing Techniques
Implementing lean manufacturing techniques can significantly reduce costs in bulk material handling operations. By focusing on minimizing waste and maximizing efficiency, businesses can streamline their processes. For example, employing value stream mapping helps identify non-value-added activities and areas where time and resources are wasted. This leads to shorter cycle times and improved throughput. Additionally, fostering a culture of continuous improvement encourages employees to suggest changes that enhance efficiency. One effective approach is to regularly review workflows and seek input from team members on how to eliminate bottlenecks. Ultimately, embracing lean principles not only saves costs but also enhances product quality and customer satisfaction.
9. Utilize Data Analytics for Insights
Data analytics can significantly enhance your understanding of bulk material handling operations. By collecting and analyzing data related to equipment performance, material flow, and labor efficiency, you can identify trends and pinpoint areas where costs can be cut. For instance, tracking the time it takes to move materials from one point to another can reveal bottlenecks in the process. If certain routes consistently take longer, adjustments can be made to pathways or equipment usage.
Moreover, key performance indicators (KPIs) can be established to monitor various aspects of your operation. Metrics such as equipment utilization rates, downtime, and energy consumption can help you assess efficiency and highlight where improvements are necessary. For example, if data shows that a specific piece of equipment is frequently underutilized, it may be worth considering if it can be repurposed or if operational schedules need adjustment.
Using predictive analytics, you can forecast future demands and adjust inventory levels accordingly, reducing excess carrying costs. This level of insight allows for proactive decision-making, ensuring that resources are utilized optimally and that waste is minimized.
10. Evaluate Supply Chain Efficiency
Evaluating your supply chain efficiency is crucial for identifying cost-saving opportunities. Start by analyzing the entire supply chain, from raw material sourcing to final product delivery. Look for inefficiencies in transportation and storage that could be driving up costs. For instance, if you’re using multiple suppliers for the same material, consolidating your purchasing could lead to better rates and lower shipping fees. Additionally, consider alternative shipping methods that may offer faster delivery at a lower cost. Implementing a robust supply chain management system can help track performance metrics and highlight areas needing improvement. By focusing on these aspects, you can streamline operations and significantly cut costs.