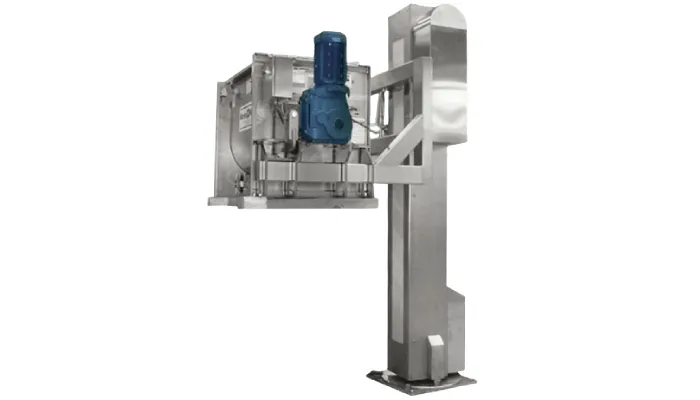
How Bulk Material Handling Equipment Saves Time?
Bulk material handling equipment helps save time by cutting down on manual labor and speeding up processes. Automated systems like conveyors and robotic vehicles handle repetitive tasks faster and more consistently than people, allowing workers to focus on complex jobs. This not only boosts productivity but also reduces errors that can cause delays. Equipment such as stackable storage solutions maximize space, so materials are easier to find and move around quickly. Additionally, automated machines lower the risk of product damage and worker injuries, preventing downtime from accidents or repairs. Predictive maintenance also keeps equipment running smoothly without unexpected stops, all adding up to more efficient operations overall.
Reduction in Manual Labor and Workforce Optimization
Bulk material handling equipment significantly cuts down the number of workers needed for tasks such as sorting and transporting materials. This reduction speeds up operations and lowers labor costs by shifting routine, repetitive, and physically demanding jobs from humans to machines. For example, conveyors and automated loaders can move heavy loads continuously without breaks, allowing employees to focus on more complex and skilled tasks that improve overall throughput. This shift not only boosts productivity but also helps businesses maintain output during labor shortages. With fewer manual steps, processes become more streamlined, reducing bottlenecks and idle time. Additionally, reducing manual labor decreases worker fatigue and the risk of injuries, which supports consistent performance and lowers absenteeism. Optimizing the workforce means employees handle specialized duties while equipment manages heavy lifting and repetitive work, creating leaner operations and faster cycle times. In the end, these improvements translate into quicker project completion and better use of resources, all while minimizing human error and sustaining steady material flow.
Streamlining Workflows with Automation
Automated conveyors, robotic arms, and guided vehicles handle materials faster and more consistently than manual labor, cutting down on slow, repetitive tasks. These systems operate continuously without breaks or fatigue, keeping workflows steady around the clock. By syncing operations across departments, automation reduces waiting times between steps and maintains a smooth, coordinated flow. Data-driven controls adjust speeds and routes in real time to optimize throughput, while integration with software systems enhances tracking and coordination of materials. This minimizes human intervention, which lowers the chances of delays and errors. Automated workflows also allow quick scaling of operations to meet changing demand without the need for extensive retraining, making the entire process more flexible and efficient.
- Automated conveyors, robotic arms, and guided vehicles move materials more rapidly and reliably than humans.
- Automation cuts down on slow, repetitive tasks by completing them faster and with consistent quality.
- Processes that took hours can be shortened significantly through automated handling and sorting.
- Automated systems work continuously, avoiding downtime caused by worker fatigue or shift changes.
- Workflow automation helps maintain smooth, synchronized operations across different departments.
- Data-driven equipment adjusts speeds and routes dynamically to optimize flow.
- Automation reduces waiting times between process steps, improving overall efficiency.
- Integrating automation with software systems allows better tracking and coordination of materials.
- Automated workflows minimize human intervention, which reduces delays and mistakes.
- Systems can scale operations up or down quickly based on demand without lengthy retraining.
Minimizing Errors for Faster Operations
Human errors in bulk material handling often lead to costly downtime and slow production lines. Automated equipment reduces these mistakes by relying on precise data and consistent processes, ensuring materials are sorted, loaded, and delivered accurately. Systems with real-time tracking quickly detect errors, preventing delays and the need for rework. Machines operate uniformly without the variability seen in manual handling, cutting down faults or misplacements. This reliability lowers troubleshooting time and speeds up the entire workflow. Automation also removes issues caused by worker fatigue or distractions, common sources of errors in manual tasks. Integrated monitoring tools provide immediate feedback, allowing quick adjustments that keep operations smooth. Fewer errors mean better product quality and less waste, which ultimately saves time across the supply chain. Together, these factors help maintain steady throughput with minimal interruptions, directly contributing to faster and more efficient bulk material handling.
Optimizing Space for Quick Material Access
Automated Storage and Retrieval Systems (ASRS) play a key role in maximizing storage density by efficiently using vertical space, which frees up valuable floor area. This allows warehouses to store more inventory without expanding their footprint, keeping materials closer to production lines and reducing replenishment time. Using stackable containers and compact equipment further shrinks the space needed for storage, creating room for other important activities. When materials are well-organized and stored in optimized layouts, picking becomes faster because workers or automated systems spend less time searching and moving items. Streamlined flow paths within the facility cut down transport distances and delays, speeding up overall operations. Space-saving designs also improve access to frequently used items, enabling quicker order fulfillment and reducing wait times, especially when automated systems can retrieve products without manual sorting. Besides speeding up processes, better space utilization leads to less clutter, lowering the risk of accidents and damage. This helps maintain a cleaner, safer environment that supports higher productivity and smoother workflow transitions throughout the facility.
Reducing Product Damage and Rework Time
Bulk material handling equipment like forklifts and conveyors handle products more gently than manual carrying, which helps prevent drops and rough handling that often lead to damage. Automation reduces human error and mishandling, lowering the chances of damaged goods that cause delays through repair or replacement. Consistent operation of these machines protects fragile or bulk materials during transfer and storage by minimizing shocks and impacts. For example, conveyors designed with smooth transitions reduce sudden jolts that can harm products. This careful handling means less time is spent on rework cycles, speeding up the overall supply chain. Additionally, less human handling lowers accident risks that could harm products. Automated inspection systems can also detect defects early, enabling quick corrections before problems escalate. By protecting product integrity, equipment supports a steady workflow without interruptions caused by faulty items, ultimately saving time and reducing costs tied to waste and returns.
Enhancing Worker Safety to Maintain Productivity
Automated bulk material handling equipment plays a key role in improving worker safety by taking over tasks that involve heavy lifting or awkward loads, which are common sources of injury. By removing employees from these risky duties, the equipment helps reduce workplace accidents and the downtime that follows for injury treatment or investigations. Safer environments mean fewer disruptions caused by accidents and less absenteeism, allowing operations to run more smoothly and consistently. Additionally, machines handle repetitive and strenuous tasks that often lead to strain injuries, helping workers avoid fatigue and maintain steady productivity throughout their shifts. Modern equipment designs also incorporate safety features such as guards and sensors, which further lower the chances of incidents. When accident rates drop, the workforce remains more stable and available, minimizing interruptions to production schedules. Automation also supports compliance with safety regulations, preventing costly penalties that could stall operations. Workers using safer, more ergonomic equipment often experience higher morale and better work quality, which contributes positively to overall productivity.
Using Predictive Maintenance to Avoid Downtime
Bulk material handling equipment equipped with IoT sensors continuously monitors performance to spot early signs of wear or potential failure. This real-time data allows maintenance teams to schedule repairs before any breakdown occurs, preventing unexpected stoppages that can halt production. Rather than performing routine checks regardless of condition, predictive maintenance targets only when necessary, saving time usually spent on unnecessary inspections. By addressing issues early, operators can make quick adjustments to avoid bigger problems that might cascade into longer downtimes. This proactive approach keeps machines running smoothly and consistently, maintaining steady workflow and handling speeds. In addition, avoiding emergency repairs means less time lost on lengthy fixes and production delays. Data-driven insights also help optimize maintenance schedules to maximize equipment uptime and extend its overall life. With fewer sudden failures disrupting operations, facilities can keep tight schedules and improve overall efficiency.
Speeding Up Order Fulfillment and Delivery
Automated bulk material handling equipment plays a key role in speeding up order fulfillment by streamlining the picking, packing, and shipping processes. By moving materials quickly and consistently, these systems reduce lead times from when an order is received to when it is delivered. For example, conveyors and automated guided vehicles (AGVs) handle large volumes efficiently, preventing bottlenecks that often slow down fulfillment centers during demand spikes. Integrated tracking systems provide real-time order updates, allowing teams to respond promptly to any changes or issues, which further reduces delays. Automation also supports around-the-clock operations, enabling faster turnaround on urgent orders without added labor costs. Streamlined workflows cut down on manual handoffs and errors, improving order accuracy and reducing time spent on returns or rework. The result is a faster delivery cycle that increases warehouse capacity, allowing more orders to be processed daily and improving overall customer satisfaction by meeting or exceeding delivery expectations.
Boosting Productivity by Reducing Worker Fatigue
Manual bulk material handling often leads to physical exhaustion, which slows down workers and increases the chance of errors. By using bulk material handling equipment, heavy lifting and repetitive motions are taken over by machines, allowing employees to keep a steady pace throughout their shifts. When workers experience less fatigue, they can maintain higher work rates and focus better on skilled tasks instead of tiring physical labor. This not only improves the speed and quality of the overall process but also supports a healthier workforce that is less likely to suffer from injuries or burnout. For example, conveyors and automated lifting devices reduce the strain of repetitive tasks, helping workers avoid common issues like muscle strain or joint pain. Reduced fatigue also boosts morale and motivation, which keeps productivity consistent and helps projects finish faster without dips caused by tired employees. With equipment handling the heavy work, employees can concentrate on more valuable activities, making the entire operation more efficient and reliable.
Attracting and Retaining Skilled Workers with Modern Equipment
Modern bulk material handling equipment plays a key role in attracting and keeping skilled workers by fostering safer, more efficient workplaces. Experienced employees are drawn to environments that prioritize their well-being and use updated technology, as this signals a company’s commitment to both productivity and worker safety. When workers have access to advanced tools, their job satisfaction tends to improve, which lowers turnover rates and saves time that would otherwise be spent on recruiting and training new staff. Training on modern systems is generally quicker and more straightforward, allowing new hires to become productive faster. Additionally, skilled workers prefer roles that reduce physical strain and hazards, which modern equipment helps achieve by automating heavy or repetitive tasks. This not only preserves worker health but also enables employees to focus on more meaningful responsibilities, enhancing morale and engagement. Retained workers develop deeper expertise over time, contributing to smoother operations and higher overall productivity. By maintaining a stable and motivated workforce, businesses benefit from consistent team performance and continuous improvement, which supports long-term operational excellence.