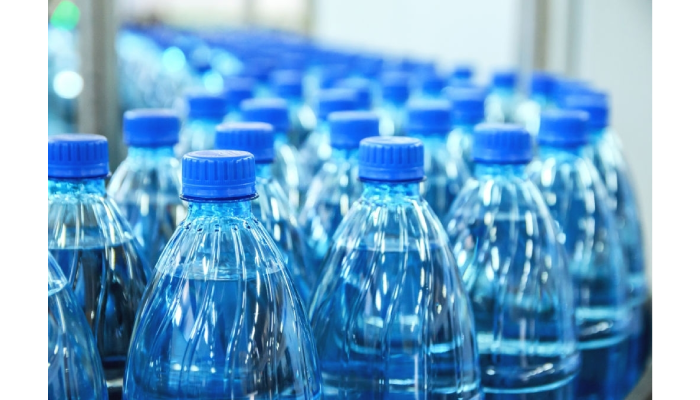
How PET Bottle Manufacturing Ensures Product Safety and Hygiene?
In today’s fast-paced consumer world, packaging plays a vital role in ensuring that products remain safe, fresh, and hygienic until they reach the end-user. Among the various materials used in packaging, PET (Polyethylene Terephthalate) bottles have gained significant popularity across industries such as food and beverages, pharmaceuticals, personal care, and household cleaning. The growing emphasis on hygiene and safety has led to stringent quality standards in PET bottle manufacturing. For any PET bottles manufacturer in India, maintaining the highest standards of cleanliness, contamination control, and structural integrity is not just a matter of regulatory compliance—it’s a core business responsibility.
Raw Material Selection and Preform Manufacturing
The journey to safe and hygienic PET bottles begins with the careful selection of raw materials. Virgin PET resins are sourced under strict quality standards to ensure there are no contaminants. These resins are then dried to remove any moisture content, which could otherwise lead to degradation of the material during molding. A leading PET bottles manufacturer in India always ensures that raw materials meet food-grade and pharmaceutical-grade criteria where applicable.
Once the PET resin is prepared, it is molded into preforms using injection molding machines. This stage requires precision and cleanliness. Manufacturing units are designed to minimize dust, foreign particles, and moisture exposure, thereby preserving the hygienic quality of the product from the very beginning.
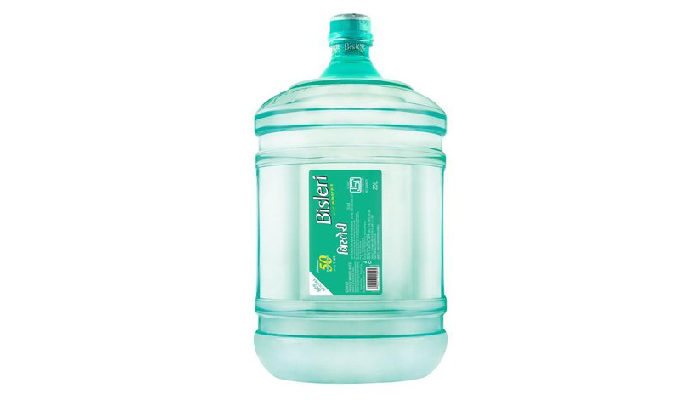
Blow Molding and Sterile Environments
The preforms are then heated and stretched into bottles using a process called stretch blow molding. For any reputed PET bottles manufacturer in India, this process is conducted in a controlled environment with specialized machinery that minimizes human contact and contamination. The machinery is sterilized regularly and often placed in cleanroom environments to maintain a sterile bottling process.
Advanced air filtration systems and proper ventilation ensure that airborne contaminants are kept at bay. The entire production line is monitored for particulate matter and bacterial presence, which is critical in industries like pharmaceuticals and food where hygiene is paramount.
Quality Control and Testing Protocols
Ensuring the safety and hygiene of PET bottles doesn’t end with manufacturing. Continuous quality control is a fundamental part of any professional PET bottles manufacturer in India. Every batch of PET bottles undergoes multiple tests, including:
- Leakage tests to ensure seal integrity.
- Drop and pressure tests to assess physical durability.
- Microbial tests to ensure sterility.
- Material compatibility tests to confirm that no leaching occurs with the stored product.
Furthermore, traceability of each batch ensures that in the rare case of a quality issue, the origin of the problem can be swiftly identified and rectified. Documentation and compliance with ISO standards, FDA regulations, and BIS certifications are standard for a credible PET bottles manufacturer in India.
Hygiene Protocols in Manufacturing Facilities
Hygiene isn’t only about the end product—it’s also about the environment in which that product is created. Reputable PET bottles manufacturers in India invest in highly sanitized manufacturing units with SOPs (Standard Operating Procedures) that are strictly followed. Employees wear protective clothing, undergo regular training in hygiene practices, and are restricted from entering certain zones without proper sanitization.
The floors, walls, and machinery are cleaned with industrial-grade disinfectants regularly. Waste is managed meticulously to avoid any risk of cross-contamination. In critical zones, such as pharmaceutical-grade bottling lines, even stricter protocols including airlocks and UV sterilization chambers are used.
Safe Handling, Packaging, and Storage
The importance of safety extends beyond manufacturing. Once the PET bottles are produced, they must be safely handled and stored to retain their hygienic quality. A competent PET bottles manufacturer in India uses automated systems to package the bottles without manual intervention. These systems use robotic arms and conveyor belts to minimize human contact.
PET bottles are packed in sterile, dust-proof packaging materials and stored in clean, pest-controlled warehouses. Temperature and humidity control is maintained in storage areas to prevent degradation of the material. The entire supply chain is managed with hygiene and safety as top priorities.
Regulatory Compliance and Sustainability Practices
Compliance with national and international safety regulations is a must for any PET bottles manufacturer in India. Organizations must follow guidelines set by the Bureau of Indian Standards (BIS), Food Safety and Standards Authority of India (FSSAI), and international norms such as the U.S. FDA and EU directives depending on the market they serve. These regulations cover aspects such as the chemical composition of the bottles, their recyclability, and the absence of hazardous substances like BPA.
Sustainability also plays a part in ensuring product safety. Many PET bottles manufacturers in India are moving towards environmentally responsible practices by incorporating post-consumer recycled (PCR) content under safe, certified procedures. This not only supports environmental goals but also ensures consumers receive safe and tested products.
Innovations and Automation Enhancing Safety
With advancements in technology, modern PET bottles manufacturers in India are integrating smart technologies such as IoT-enabled quality checks, AI-powered defect detection systems, and robotic automation to further enhance the safety and consistency of their bottles. Real-time monitoring and predictive maintenance help prevent downtime and contamination risks, ensuring a smoother and cleaner production process.
Innovation in bottle design also contributes to hygiene. Features like tamper-evident caps, UV-resistant coatings, and ergonomic grip designs are created not only for user convenience but also for added protection against contamination and damage during transit.
Conclusion
The meticulous processes followed by a dedicated PET bottles manufacturer in India demonstrate a robust commitment to safety, hygiene, and quality. From raw material selection to final delivery, every stage of the PET bottle production process is governed by strict standards and quality checks designed to ensure that the end-user receives a product that is clean, safe, and reliable.
Whether used in packaging drinking water, storing life-saving medications, or delivering personal care products, PET bottles must meet the highest hygiene criteria. Manufacturers in India are not just keeping up with these expectations—they’re setting global benchmarks. As the demand for safer packaging continues to rise, the role of a responsible PET bottles manufacturer in India becomes increasingly essential in safeguarding public health and ensuring consumer trust.
Resource URL: