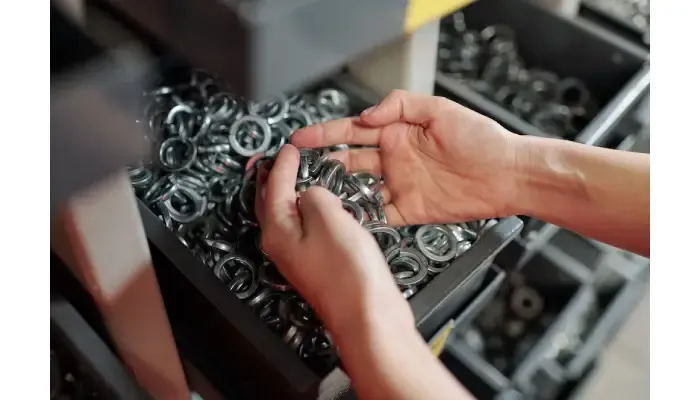
Innovations in Fasteners Manufacturing: What to Expect in 2025?
The fastener manufacturing industry is poised for exciting changes by 2025. With advancements in materials, the use of titanium alloys and carbon composites will offer high-performance fasteners that shine under pressure. Meanwhile, additive manufacturing and 3D printing promise quicker, customized solutions. Robotics and automation will boost efficiency, while AI enhances monitoring capabilities to predict maintenance needs. Sustainability will take a front seat as manufacturers adopt eco-friendly materials and lean processes. As the market grows globally, innovations like smart fasteners integrated with IoT technology could redefine maintenance practices. Overall, embracing these trends is vital for staying competitive in this evolving landscape.
1. High-Performance Fasteners and Material Advancements
The fasteners manufacturers in India are shifting towards high-performance solutions by utilizing advanced materials such as titanium and carbon composites. These materials offer enhanced strength, making them ideal for demanding applications in sectors like aerospace and automotive. Corrosion-resistant coatings are becoming standard, significantly improving the longevity of fasteners in harsh environments. There’s also a notable focus on lightweight fasteners that maintain durability, which is crucial in industries where weight savings can lead to improved efficiency and performance.
Nanotechnology is paving the way for the development of even stronger and lighter fasteners, allowing manufacturers to push the limits of what’s possible. By exploring new alloys designed for extreme temperatures, the industry is addressing the needs of high-stress applications. Collaboration with universities and research institutions is fostering innovation in material science, leading to smarter materials that can adapt to changing environmental conditions. As a result, manufacturers are emphasizing certifications and standards to ensure the quality and reliability of these advanced materials, preparing for a future where performance is paramount.
- Increased use of advanced materials like titanium and carbon composites for enhanced strength.
- Focus on corrosion-resistant coatings to improve longevity in various environments.
- Development of lightweight fasteners that do not compromise on durability.
- Utilization of nanotechnology to create stronger and lighter fasteners.
- Adoption of aerospace-grade materials for high-stress applications.
- Exploration of new alloys to improve performance in extreme temperatures.
- Integration of innovative manufacturing techniques to enhance material properties.
- Research into smart materials that can adapt to changing conditions.
2. The Role of 3D Printing in Fastener Production
3D printing is transforming fastener production in exciting ways. One of its key advantages is the significant reduction in lead times for creating custom fasteners. This technology allows manufacturers to produce unique designs that traditional methods simply can’t achieve, thanks to its ability to create complex geometries.
Another major benefit is the reduction in material waste. Unlike subtractive manufacturing processes, additive manufacturing employs precise techniques that use only the necessary amount of material, leading to a more sustainable production method. Additionally, with on-demand printing capabilities, companies can minimize inventory costs by producing fasteners as needed rather than maintaining large stockpiles.
As 3D printing technology evolves, the exploration of various material options is becoming more common. Manufacturers can now experiment with different plastics, metals, and composites tailored for specific applications. Enhancements in print speed and precision are also noteworthy, facilitated by new printer technologies that make production faster and more accurate.
Moreover, the integration of advanced software for design optimization is aiding in the development of better fasteners. This technology supports rapid iteration and allows for swift design changes during the prototyping phase, which is crucial in industries that require constant innovation.
Collaboration with various sectors is also on the rise. Industries are partnering with fastener manufacturers to develop specialized fasteners using 3D printing, catering to unique needs across sectors like aerospace and automotive. To keep pace with these advancements, training programs for engineers on 3D printing technologies and techniques are becoming essential, ensuring the workforce is well-equipped to harness the full potential of this innovative manufacturing process.
3. Automation and Robotics in Fastener Manufacturing
The fastener manufacturing industry is increasingly leaning towards automation and robotics to boost efficiency and reduce labor costs. By implementing robotics in assembly lines, manufacturers can achieve higher precision and faster production rates, minimizing the reliance on manual labor. Automated inspection systems are also becoming more common, ensuring quality control and consistency in every batch produced.
Collaborative robots, or cobots, are being introduced to work alongside human workers, enhancing productivity while maintaining a safe working environment. These robots can perform repetitive tasks, allowing human operators to focus on more complex issues that require critical thinking. Furthermore, the integration of machine learning algorithms is making it possible to optimize production efficiency, predicting potential bottlenecks and adjusting processes in real-time.
Real-time data analytics is transforming how manufacturers monitor their production processes. This technology allows for remote monitoring of machinery and equipment, providing insights that help in maintaining optimal performance. Customizable automation solutions cater to different manufacturing scales, making it easier for businesses of all sizes to adopt these advancements.
By reducing human error through precision automation, manufacturers can improve their overall output quality. Additionally, the development of advanced software for scheduling and resource allocation streamlines operations, ensuring that resources are utilized effectively. As automation becomes more prevalent, a strong focus on safety protocols is essential to protect both human workers and equipment, ensuring a seamless integration of technology in manufacturing environments.
4. Sustainability Trends in Fasteners
The fasteners manufacturing industry is making significant strides toward sustainability, reflecting a growing commitment to environmental responsibility. One key trend is the increased use of recycled materials in production. Manufacturers are now creating fasteners from previously used metals and plastics, reducing the demand for virgin resources and minimizing waste. Additionally, there is a push for biodegradable coatings that can reduce the environmental impact of fasteners at the end of their life cycle.
Energy-efficient manufacturing processes are also gaining traction. Techniques such as lean manufacturing focus on minimizing energy consumption and waste, leading to a smaller carbon footprint. To support these efforts, companies are adopting life cycle assessments to evaluate the environmental impact of their products from production to disposal.
The exploration of circular economy principles is reshaping fastener design. This approach encourages the creation of products that can be reused or recycled, contributing to a more sustainable production cycle. Collaborations with suppliers for sustainable sourcing of raw materials further enhance these initiatives, ensuring that the entire supply chain prioritizes eco-friendly practices.
Packaging is another area seeing innovation, with manufacturers promoting eco-friendly solutions that reduce plastic waste. Furthermore, many companies are investing in renewable energy sources for their manufacturing facilities, aiming for long-term goals of carbon neutrality in their production processes.
Community engagement is also an essential aspect of this trend. Companies are participating in initiatives that raise awareness about sustainability, fostering a culture of environmental responsibility within the industry. As the fastener sector moves forward, these sustainability trends will play a pivotal role in shaping its future.
5. Smart Fasteners and IoT Integration
smart fasteners are set to revolutionize the way we monitor and maintain critical connections in various industries. By integrating sensors directly into fasteners, manufacturers can track performance metrics such as load, temperature, and even signs of corrosion in real time. This data not only helps in assessing the current condition of fasteners but also plays a crucial role in preventive maintenance. For instance, companies can develop mobile applications that provide instant access to this data, allowing engineers to make informed decisions without needing to inspect each fastener physically.
Predictive analytics further enhances this capability by enabling maintenance schedules based on actual usage patterns and environmental conditions. Imagine a scenario where a fastener in a bridge beams alerts the maintenance team about unusual stress levels, allowing for timely interventions that prevent catastrophic failures. Additionally, ongoing monitoring boosts safety standards, as potential issues can be identified before they escalate into serious problems.
Collaboration between fastener manufacturers and tech firms is driving innovations in IoT solutions. Research is also underway to improve wireless communication methods, making smart fasteners compatible with existing industry systems. This compatibility ensures that companies can integrate new technologies without overhauling their current infrastructure.
Moreover, the emphasis on cybersecurity is paramount as the industry moves towards digitization. Data integrity must be protected against potential breaches, making it essential for manufacturers to adopt robust security measures. As smart fastener technologies evolve, developing industry standards will become crucial to ensure interoperability and reliability across various applications, paving the way for a future where remote diagnostics and troubleshooting become routine.
6. Market Growth and Supply Chain Innovations
The fastener market is poised for rapid growth, particularly in emerging economies where industrialization is accelerating. As sectors like aerospace, automotive, and renewable energy expand, there’s a growing demand for high-performance fasteners that can withstand harsh conditions and meet stringent safety standards. To keep pace, manufacturers are increasingly leveraging digital tools, such as blockchain technology, to enhance transparency and traceability in supply chains. This shift not only improves trust between suppliers and clients but also helps in tracking materials and products more effectively.
Additionally, artificial intelligence is making waves in demand forecasting, allowing companies to predict market trends and adjust their production strategies accordingly. This proactive approach can significantly reduce lead times, which is essential as just-in-time (JIT) inventory practices gain traction. By collaborating with logistics providers, companies can streamline their supply chain processes, ensuring that they meet customer demands promptly.
Investments in digital platforms for order management are also transforming how businesses interact with their customers. These platforms facilitate smoother transactions and better communication, thus enhancing overall efficiency. Furthermore, the exploration of alternative materials is becoming increasingly important to mitigate supply chain disruptions, ensuring that manufacturers can continue to deliver quality products even in challenging circumstances. Partnerships across the globe will further enhance market reach, enabling companies to adapt to the evolving landscape and meet the diverse needs of their clients.
7. Emerging Trends and Collaborations in Fasteners
The fasteners industry is experiencing a notable shift towards collaborative innovation. Manufacturers are increasingly partnering with end-users to co-develop fasteners tailored for specific applications. This trend is particularly evident in niche markets such as medical devices and electric vehicles, where customized solutions are essential for performance and safety.
Joint ventures are becoming more common as companies seek to leverage each other’s technology and resources. For instance, collaborations with tech startups are introducing fresh ideas and cutting-edge technologies that drive product innovation.
Networking events play a crucial role in fostering these connections, allowing industry players to share knowledge and explore potential partnerships. Academic collaborations are also on the rise, focusing on research and development to push the boundaries of fastener technology.
Moreover, there is a growing interest in smart fasteners that integrate with IoT systems, enhancing monitoring and maintenance capabilities. Companies are engaging with tech firms to create these advanced solutions, ensuring that fasteners can meet the demands of modern applications.
Participation in industry associations is vital for staying updated on emerging trends and best practices, further propelling the industry’s evolution.
8. Industry Events and Networking Opportunities
Industry events will play a crucial role in shaping the future of fastener manufacturing, especially with the anticipated Fastener Fair Global 2025 taking center stage. Scheduled for March 25-27, 2025, in Stuttgart, Germany, this event promises to be a significant gathering for industry professionals, showcasing the latest innovations and providing ample networking opportunities. Trade shows like this not only allow companies to present their new products but also facilitate workshops and seminars focused on skill enhancement and knowledge sharing.
Panel discussions featuring industry leaders will delve into current trends, offering insights that can help businesses adapt to changing demands. Networking events will be essential for building relationships and partnerships, fostering collaboration that can drive future innovations. Additionally, exhibitions will highlight advancements in fastener technology, providing a platform for startups to showcase their breakthroughs.
The rise of online platforms has also transformed networking, enabling virtual discussions and connections that transcend geographical barriers. Competitions to promote innovation in fasteners will encourage creativity and advancement, making these industry events not just opportunities for learning, but also for inspiring the next generation of fastener technology.
9. Focus Areas for Fastener Manufacturers
Fastener manufacturers are gearing up to tackle the evolving landscape of production and market demands. A primary focus is the development of fasteners that can keep pace with high-speed manufacturing processes. This means investing in research and development to explore new technologies and materials, such as advanced alloys that enhance strength and corrosion resistance. Manufacturers are also prioritizing product quality, implementing stringent testing protocols to ensure reliability in various applications.
Automation is another key area of focus, with manufacturers exploring robotic solutions that can streamline production lines and improve efficiency. By adopting lean manufacturing principles, companies aim to minimize waste and optimize resources, creating a more sustainable production model. Customer feedback is becoming increasingly important as manufacturers look to refine their offerings and align with market trends. This customer-centric approach often leads to innovative solutions that meet the specific needs of various industries.
Furthermore, workforce development plays a crucial role in these innovations. Manufacturers are investing in training programs to equip workers with the skills needed to operate new technologies effectively. This investment not only enhances productivity but also fosters a culture of continuous improvement.
Sustainability is a major focus as well, with manufacturers engaging in initiatives that align with consumer expectations for eco-friendly practices. Building a resilient supply chain is essential for adapting to market changes and ensuring that production can continue smoothly despite external disruptions. All these focus areas reflect a commitment to advancing the fastener industry, positioning manufacturers to thrive in the dynamic environment of 2025.
Frequently Asked Questions
1. What new technologies are being used in fastener manufacturing?
In 2025, we can expect to see advanced techniques like 3D printing and automation in fastener manufacturing. These technologies help make production faster and more precise.
2. How will sustainability affect fastener production in the future?
Sustainability will play a key role, with manufacturers focusing on eco-friendly materials and processes. This means using recycled materials and minimizing waste.
3. What types of fasteners might be on the rise by 2025?
In the near future, specialized fasteners for specific industries, like aerospace and automotive, are likely to gain popularity. These fasteners will be designed for better performance and reliability.
4. How is the demand for smart fasteners changing the industry?
Smart fasteners, which can monitor conditions and provide data, are becoming increasingly important. This trend is driving innovation to enhance product functionality in various applications.
5. What role will automation play in fastener manufacturing by 2025?
Automation is set to significantly streamline the fastener manufacturing process. By 2025, more companies will likely adopt robotic systems to improve efficiency and reduce human error.
TL;DR The fastener manufacturing industry is set for transformation by 2025, driven by advancements in high-performance materials, 3D printing, and automation. Sustainability efforts are leading to eco-friendly fasteners and manufacturing processes. The integration of smart technology and IoT is enhancing monitoring and predictive maintenance capabilities. Market growth is expected, with innovations in supply chains and collaborations focused on customization. Upcoming industry events, like the Fastener Fair Global 2025, will provide networking opportunities. Manufacturers will need to adapt to modern manufacturing demands and invest in new technologies to stay competitive.